Premium Quality for Your Success
We set ourselves the highest quality standards. To ensure the maximum performance of our products we use simulations and laboratory tests.
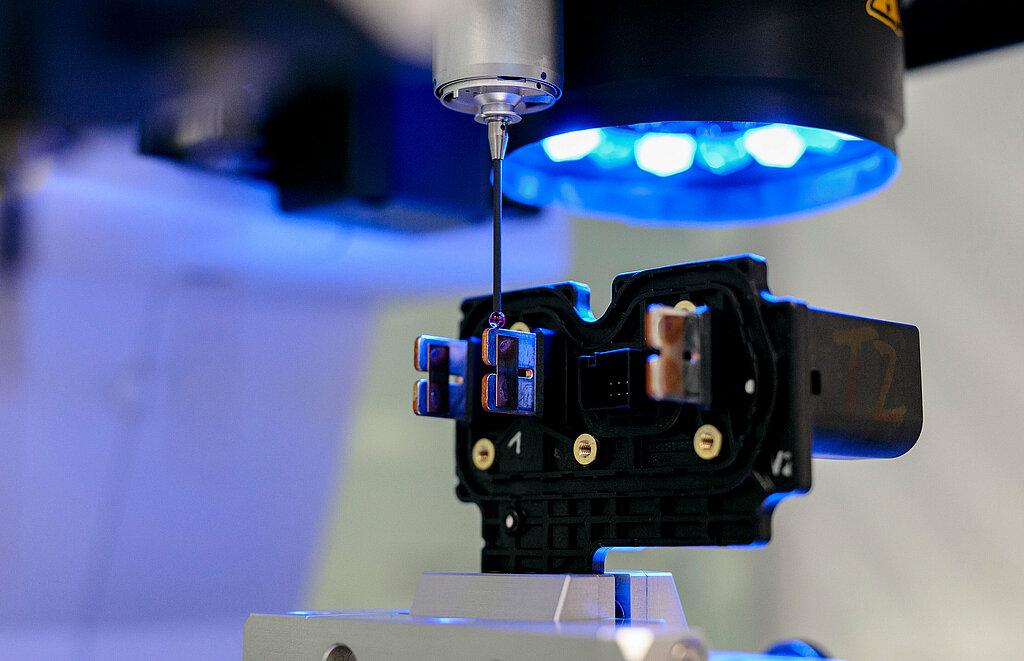
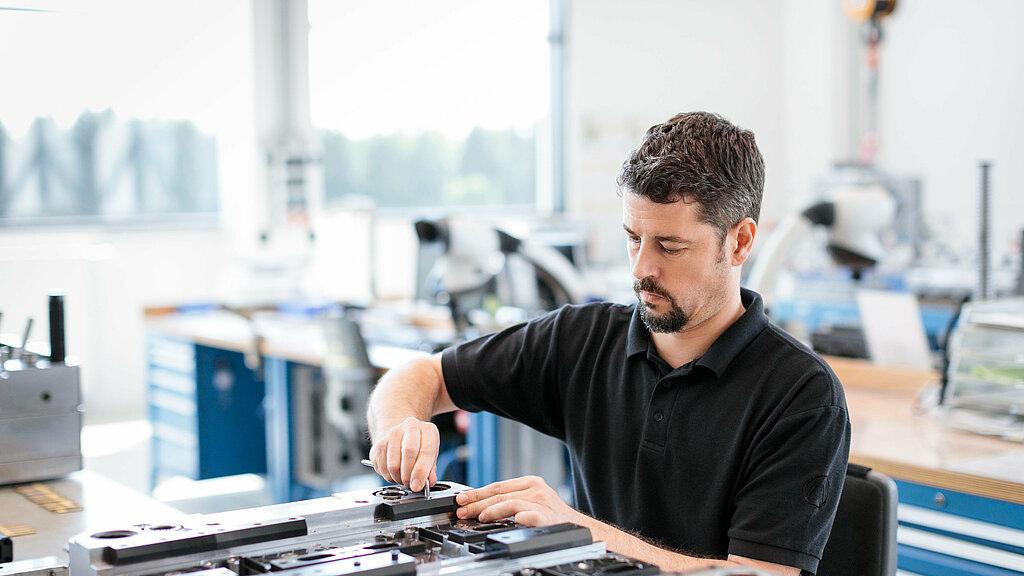
Quality Is Our Top Priority
Our materials, procedures and processes are continuously evaluated and adapted to latest standards. Furthermore, certified quality is a matter of course at all our locations worldwide. We are certified to the standards IATF 16949, ISO 14001, ISO 45001 and ISO 9001 and the Authorised Economic Operator (AEO) guidelines.
The satisfaction of our customers is equally important to us: More than 500 employees work for our certified quality management worldwide. We are constantly investing in the expansion of technology, resources and know-how.
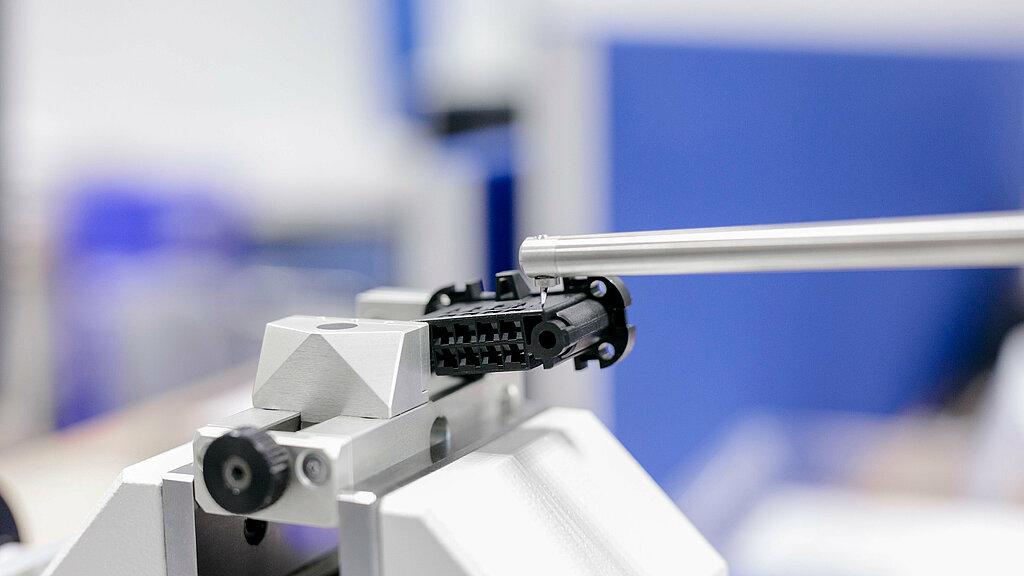
Quality Check at Every Step
An integral part of our development philosophy is the seamless testing and qualification of all components – from the design and construction phase to series-production readiness. We apply state-of-the-art simulations and laboratory tests all the time. In this way, we guarantee the maximum performance of our products throughout their entire life cycle.
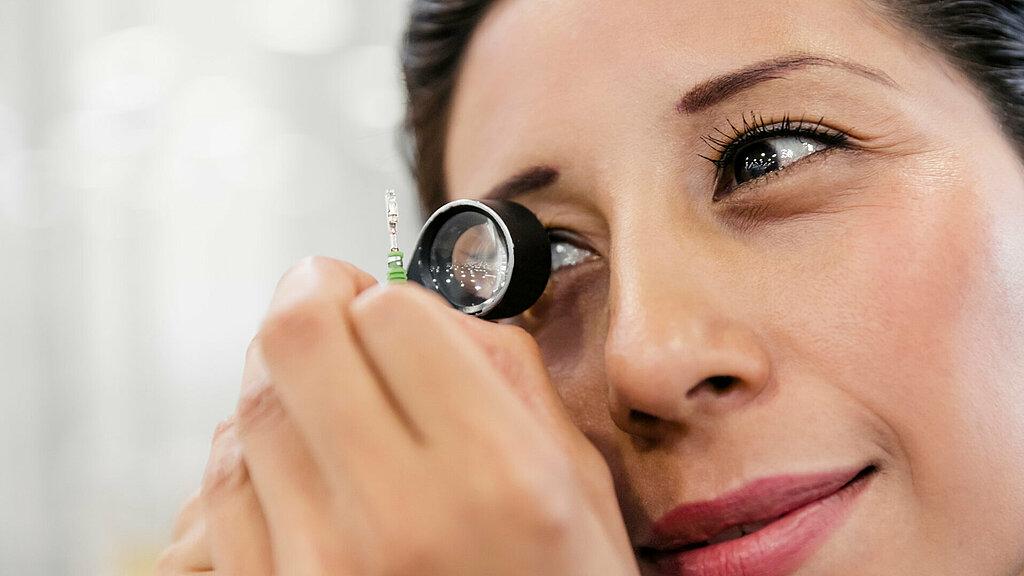
Through Heart and Hand to Premium Solutions
The automotive industry demands a high level of product quality. Therefore, employees of the quality department are already involved in inquiries for new projects. In this way, the fulfillment of customer requirements can be ensured at an early stage. At the same time, Hirschmann Automotive sets great value on the sound training of its quality specialists. This is how we meet our customers on a level playing field.
An Extract of Our Analyses
Simulation of dynamic loads as sine vibration, random vibration and shock simulation coming from engines directly or from the the usage of parts in automotive vehicles.
"Look into the Detail" - down to the micrometer range for the analysis of surface contaminations, abrasion or fractographic analyses.
Cross-Section analysis to evaluate the quality of welding joints, soldering joints or other metallic connections.
Vacuum tests with helium or negative/positive pressure tests with air for leakage analysis.
High-resolution resistance measurements, insulation resistance tests, high-current load simulations; high-voltage resistance tests.
Grafical “hot-spot” analysis to identify the critical areas in high current load applications.
Simulate environmental loads as temperature shock tests, heat or cold tests, salt-spray tests, fluid shock simulation.
Non-destructive damaged part analysis or measurement of components.
Mechanical analyses for push/pull forces to assess the fracture behavior or the mechanical strength of components.
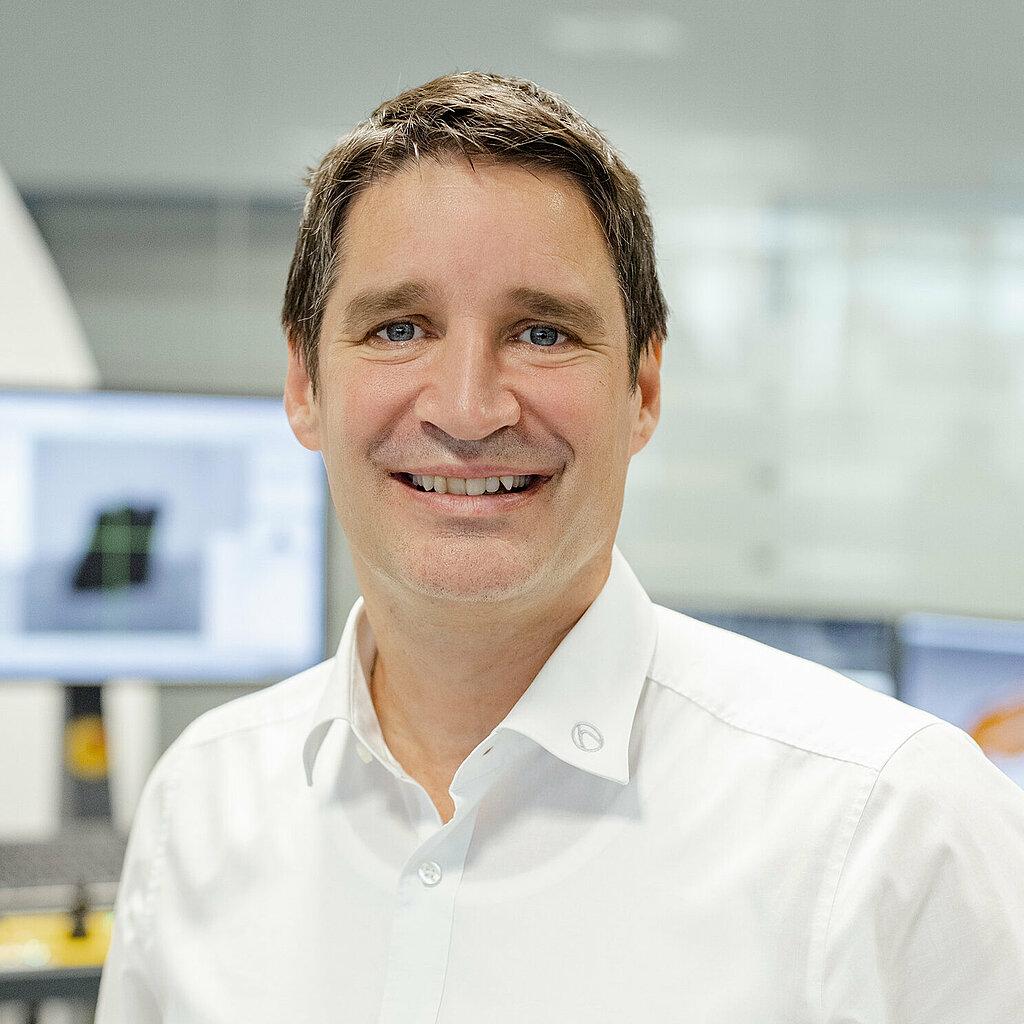
Matthias Bell
Matthias Bell, Quality Director
The New Technical Cleanliness Area in Târgu Mureș
New Technical Cleaniness Area | in Târgu Mureș